
METAL STAMPING GLOSSARY
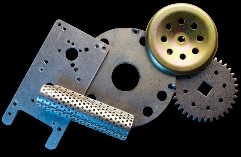
With 50+ years of metal stamping experience, Service Stampings is a trusted source for stampings, as well as of information and advice for its customers.
We're pleased to offer a glossary of metal stamping terms as a service to our customers and others in the industry.
If you're looking for an experienced, knowledgeable metal stamping provider, you're looking for Service Stampings. Contact us now to put our expertise to work on your next project.
ANNEALING: Softening or strain relieving of the material by application of heat above the critical temperature for the correct time interval, then cooling slowly enough to avoid hardening.
BEAD:
a) Narrow ridges in a part for reinforcement.
b) Narrow ridges along the edge of a part, and corresponding ridges in the die to improve holding action in press working.
BLANK: The piece of sheet material, usually flat, produced in cutting dies, and usually to be subjected to farther press operations.
BLANK DEVELOPMENT: Because of stretching and ironing present in drawing and forming operations, it is usually necessary to arrive at the blank size and shape by trial and error. The drawing and forming dies, therefore, are made first and when the blank size and shape are finally determined the blanking die is made last.
BLANKING DIE: A die used for shearing or cutting blanks usually from flat sheets or strips. The single blanking die used for producing one blank at each stroke of the press is the simplest of all dies, consisting essentially of punch, die block, and stripper.
BRAKE BENDING OR PRESS: A form of open frame, single action press comparatively wide between the housings, with had designed for holding long narrow forming edges or dies. It is used for bending and forming strips and plates.
BURR: A rough ridge, edge, protuberance, or area, as that left on metal after cutting, drilling, punching, etc.; in stamping it occurs in cutting dies because of the clearance between punch and die.
BURR SIDE: This generally refers to the side or face of a blank or other stamping which comes in direct contact with the punch in a blanking operation, and the side or face of a blank or other stamping which comes in direct contact with the die in piercing or perforating operations.
CAPACITY OF A PRESS: The rated capacity of a press is the tons pressure which the slide will safely exert at the bottom of the stroke in doing work within the range of the press.
COINING: A squeezing operation, usually performed cold in a closed die, in which the metal is forced to flow to fill the shape and profile of the dies. The term is also applied loosely to other very severe and localized cold forming operations. It is usually done in a Knuckle Joint or Coining Press.
COLD ROLLED SHEETS: Steel sheets processed to produce a surface superior to a hot rolled, pickled finish. In the present basic treatment, the hot rolled sheets or coils are pickled, cold reduced in thickness and usually annealed, temper or skin rolled and roller leveled.
COMBINATION DIE: A press tool for doing two or more operations at each stroke of the press, one performed inside of the other. They are most frequently blanking and drawing operations.
COMPOUND DIE:
a) Tool for two cutting operations, one performed inside of the other, e.g., die for blanking and piercing a washer.
b) A die in which blanking, forming; or drawing operations are combined.
DEGREASING: Solvent cleaning is perhaps the most effective method of removing grease or oil films. The action is purely mechanical, no chemistry or electricity is involved. The solvent dissolves the grease or oil and thereby removes it from the metal. Two general types of organic solvents are used in industry: petroleum solvents, which are namable, and chlorinated solvents, which do not present a fire hazard.
DIE:
(a) A complete tool used on a press for any operation or series of operations, such as, forming, impressing, piercing and cutting. The upper member (or members) are attached to a slide (or slides) of the press, and the lower member is clamped or bolted to the bed or bolster, the die members being so shaped as to cut or form material placed between them when the press makes a stroke.
(b) The female part of a complete die assembly as described in (a).
(c) A tool for cutting external threads.
DIE SET: A standardized tool or tool holder consisting of die base to which a die is to be attached, and punch plate to which a punch is to be attached. The base and plate are held in accurate alignment by guide pins or posts and bushed guides.
DOUBLE ACTION DIE: In the usual double action draw die, the blank holder (or hold-down) is fastened to the blank holder slide (outer slide), the punch is fastened to the plunger (inner slide), and the die is fastened to the bolster (or bed). The double action drawing operation is essentially as follows: The blank holder moves first and securely holds the outer edges of the blank against the mating part of the die at which time the punch starts the draw. At the completion of the draw, the punch starts back first, followed by the blank holder which has remained stationary, holding the blank during the entire draw.
DRAW RING:
(a) See blank holder or hold-down (preferred meaning).
(b) Ping shaped die part, either die ring itself or separate steel ring over inner edge of which, punch draws the part.
DRAWING: A variety of forming operations, such as, deep drawing a sheet blank, redrawing a tubular part, and drawing rod, wire and tube. The usual drawing process in reference to the working of sheet metal in a press is a method for producing a cup-like form from a sheet metal disc by holding it firmly between blank holding surfaces to prevent formation of wrinkles while punch travel produces the required shape.
FIXTURE: A tool or device for holding and accurately positioning a piece or part on a machine tool or other processing machine.
FLAME-HARDENING: A heat-treating method for surface-hardening of steel of the proper specifications in which an oxyacetylene flame heats the surface to a temperature at which subsequent cooling, usually with water or air, will give the required surface hardness.
FORMING: Any change in the shape of a metal piece which does not intentionally reduce the metal thickness.
HOT ROLLED SHEETS: Steel sheets reduced to required thickness at a temperature above the point of scaling and therefore carrying hot mill oxide. They may he flattened by cold rolling without appreciable reduction in thickness or by roller leveling or both. Depending on the requirements, hot rolled sheets can be pickled to remove hot mill oxide and are so produced when specified.
HYDRAULIC PRESS: A press whose slide or ram is actuated by a hydraulic cylinder and piston whose pressure is obtained from a hydraulic pump. The press cylinder, the pump, and the fluid (usually oil) under pressure, together with connecting valves and controls form a hydraulic system which theoretically acts in accordance with the hydraulic principle.
INCLINABLE (O.B.I.) PRESS: Small and medium size crank presses which may be inclined (tilted backward) to facilitate ejecting of finished parts by gravity. These presses are usually of the open-back, gap type frame with right to left crankshaft. They are built in a maximum size of about 200 tons. They may be, and very often are, used in the upright or vertical position, being readily adjustable, usually by a hand mechanism, to any desired inclination up to the usual maximum of 450. The inclinable press is the most widely used type of press, being particularly adapted for blanking, piercing, forming and shallow drawing operations on a multitude of small and medium size parts. This type of press frequently is equipped with mechanical feeds for rapid automatic production.
IRONING: The press operation of reducing the wall thickness, of a shell while retaining the original thickness of the bottom, and reducing the inside diameter by only a small amount. It is the opposite of a true drawing operation in which reducing the diameter is the primary consideration, and wall thickness may even be increased slightly.
MECHANICAL PRESS: A press whose slide or ram is operated by a crank, eccentric, cam, toggle links or other mechanical means, as contrasted to fluid or other means.
MILL EXTRAS: Are the charges above base price for sheet such as gage extra, width extra, length extra, pickling and oiling extra, etc.
MULTIPLE SLIDE (OR PLUNGER) PRESS: Presses with multiple slides are built in two general types:
(a) In which individual slides are built into the main slide in order to provide an individual adjustment for each set of tools.
(b) In which individual slides have individual connections and cranks or eccentrics on the main shaft. This arrangement provides means for variations in length of stroke and timing as well as adjustment.
Multiple slide presses are usually equipped with transfer feeds or double roll feeds for automatic, progressive die production of stampings.
PERFORATING: The piercing of many holes, usually identical and arranged in regular pattern, in a sheet, blank or previously formed part. The holes are usually round, but May be of any other shape. The operation is also called multiple piercing. See Piercing.
PIERCING: The general term for cutting (shearing or punching) openings, such as holes and slots in sheet material, plate or parts. This is practically the same operation as blanking, the difference being that the slug or piece produced by piercing is scrap, whereas the blank produced by blanking is the useful part. In the two cases the burr is opposite. See Purr Side.
PROGRESSIVE DIES: A series of two or more dies arranged in line for performing two or more operations on a part, one operation (single or compound) being performed in each die, that is at each station. Work in the form of, strip is usually fed to progressive dies automatically by a roll feed, or blanks or parts are fed by a transfer feed.
PUNCH: n. (a) The male part of a die, as distinguished from the female part called the die. The punch is usually the upper member of the complete die and thus mounted on the slide, (except in the inverted die). See Inverted Die.
(b) In double action, dies, the punch is the inner portion of the upper die, is mounted on the plunger (inner slide) and does the drawing.
v. To pierce a hole, also called punching.
REDRAWING: Second and following deep drawing operations in which the cup-like shells are deepened and reduced in cross-sectional dimensions (sometimes in wall thickness). Redrawing is done in both single action dies and in double action dies.
RESTRIKING: A sizing or light coining operation in which compressive strains are introduced in the stamping to counteract or offset tensile strains set up in previous operations. For example, re-striking is used to counteract spring-back in a bending operation.
ROLL FEED: A mechanism for feeding strip or sheet stock to a press or other machine. The stock passes between two revolving rolls mounted one above the other, which feed it under the dies in a predetermined length at each stroke of the press. Two common types of drive are the oscillating lever type and the rack and pinion type.
The single roll feed may be used to either push or pull the stock to or from the press. The double roll feed is commonly used with wider presses (left to right) or in other cases where a single roll feed is impractical.
RUN: Is the quantity of parts produced in one set-up.
SHEAR:
(a) n. A machine or tool for cutting metal and other material by the closing motion of two sharp closely adjoining edges; e.g., squaring shear and circular shear.
(b) v. To cut by shearing dies or blades, as in a squaring shear.
SHEET: Any material or piece of uniform thickness and of, considerable length and breadth as compared to its thickness is called a sheet or plate. In reference to metal such pieces; less than 1/4" thick are called sheets and 1/4" thick and over are called plates.
SPINNING: The formation of sheet metal or tubing blanks into circular-shaped parts by means of a lathe, form blocks or chucks and hand tools or other forming tools which serve to press and shape the revolving metal shout the revolving form, is known as spinning. Many kitchen utensils, lampshades, and chandelier parts are examples of spinning. Besides forming, spinning operations include trimming, curling, beading and bulging.
SPRING BACK: The extent to which metal naturally tends to return to its original shape or position after undergoing a forming operation. This is compensated for by "over-bending" or by a secondary operation of re-striking (squeezing).
TRIMMING: A secondary cutting or shearing operation on previously formed, drawn or forged parts in which the surplus metal of an irregular outline or edge is sheared off to form the desired shape and size.
SHORT RUN STAMPING | FABRICATION | SECONDARY OPERATIONS | ASSEMBLY & FINISHING | QUALITY ASSURANCE | INDUSTRIES SERVED
CAPABILITIES | NEWS | FAQs | LITERATURE | GLOSSARY OF TERMS | SITE MAP